Technology That Revolutionizes the Use of Real Wood
The wood market has shifted towards alternative materials, diverting attention from wood despite its status as a fundamental building material. Many have opted for substitutes to avoid common issues. But we know, selecting the right type of wood, utilizing proper production methods and advanced technology can resolve these challenges, allowing builders and homeowners to reap the benefits of using genuine wood.
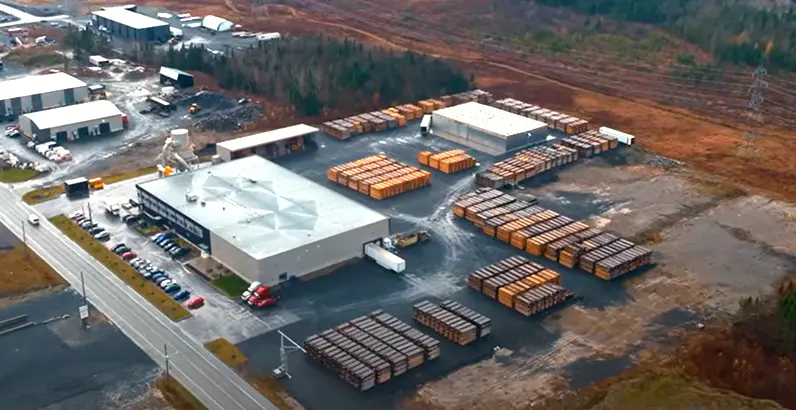
How We Push the Envelope of Innovation
We continually evolve our state-of-the-art facilities while making significant investments in cutting-edge equipment that uses artificial intelligence to optimize raw material usage across 210,000 square feet in two manufacturing plants.
The Better Wood: How We Create Princeton Fine Wood Products
It Starts with Eastern White Pine
Why replicate nature, when you can use it. Impressive in stature, Eastern White Pine trees dominate the forests where they are planted, which is why it is nicknamed “The King of the Forest.” Naturally rot-resistant and well-adapted to the harsh climate of the northeast, these attributes lend to the longevity, stability, performance, and workability of Princeton Fine Wood products.
Sourced locally from Maine, Vermont, New Hampshire, and New York, all our raw material is traceable, sustainably forested, and part of a supply chain that reduces transportation, maximizes material usage, and waste recuperation. We also own our sawmill in Tupper Lake, New York, to meet the growing needs of customers better and ensure a consistent supply of raw materials.
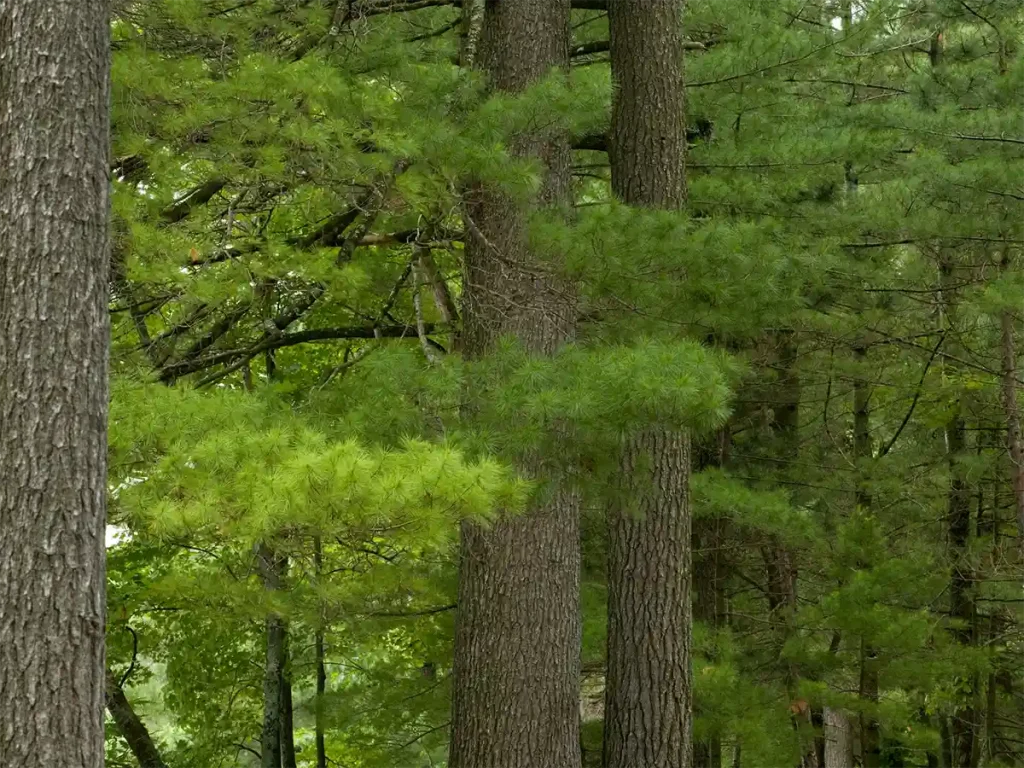
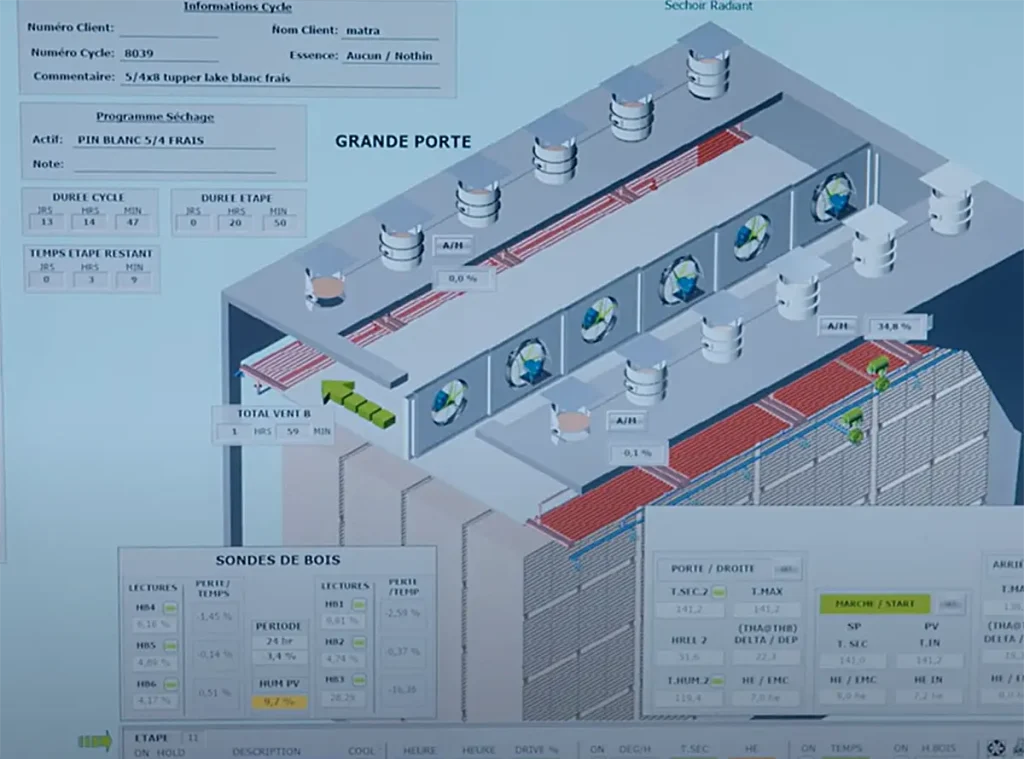
The Drying Process
Our Eastern White Pine lumber bundles are selected and placed in drying cells powered by sawdust generated from our manufacturing process. The humidity and temperature are closely monitored in real time to ensure consistent and precise finely crafted wood. Depending on the dimensions of the lumber, the drying cycle will vary between 12 and 21 days. As the desired moisture content approaches, a balancing cycle will ensure even moisture content throughout. Once dry, the wood is stored in a weatherproof location, waiting to be processed into finger-jointed boards.
Planing and Cross Cutting
Planing is the first stage of manufacturing finger-jointed products. Once planed, each plank of wood is scanned to identify the grade and defects. The lumber is then cut into sections to eliminate defects such as knots, splits and resin pockets. At this stage of the process, we validate the moisture content of the boards, ensuing uniform moisture content along their entire length, giving our products a superior dimensional stability.
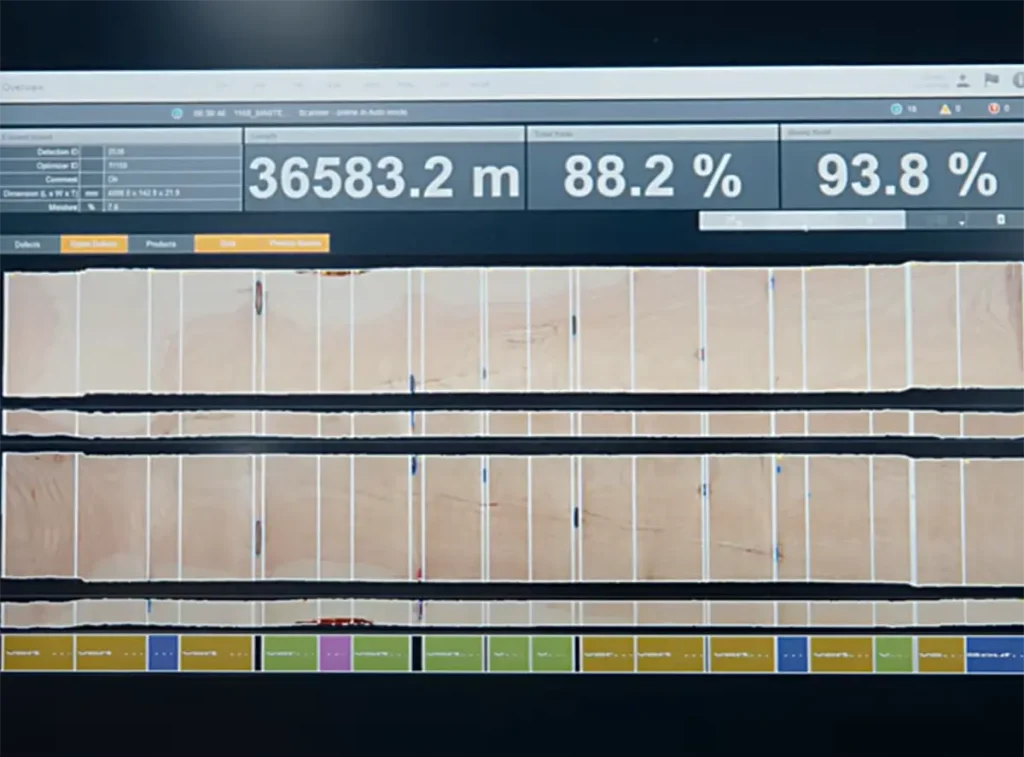
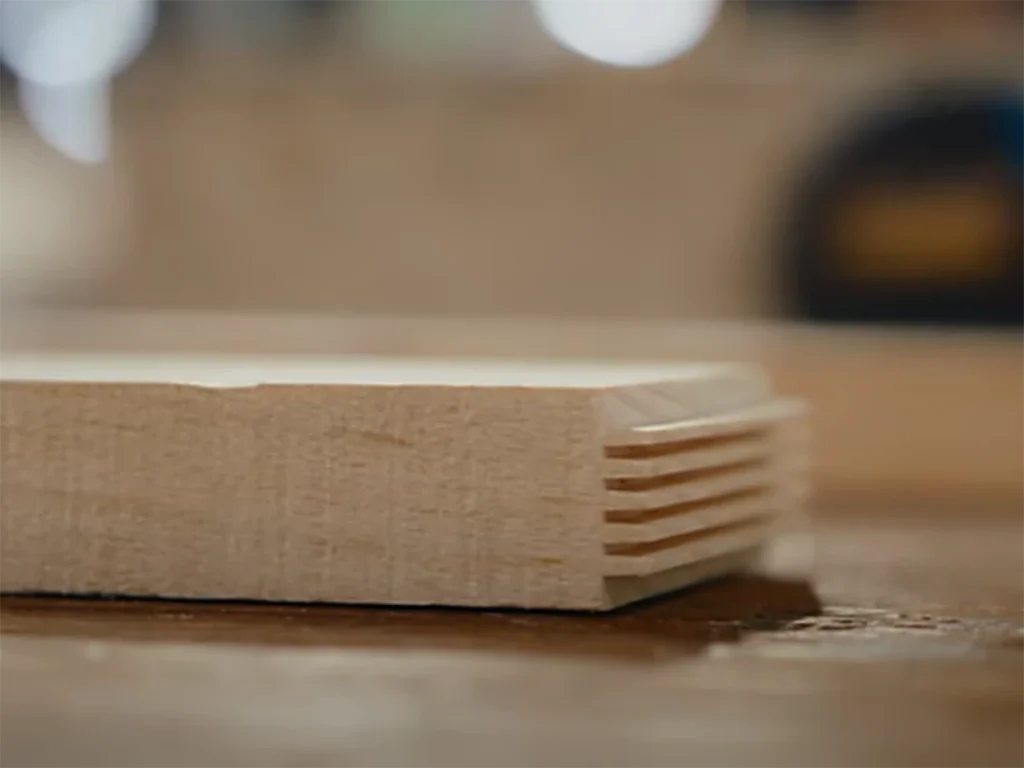
Finger-Jointing
At the jointing stage, the ends of the selected wood sections are machined and butt-jointed into 16′ long pieces. Precision is crucial to obtain a perfectly closed joint with no gaps. During machining, a shoulder is created on each of the two surfaces so only a straight joint line is visible. Precision is crucial and must be accurate to obtain a perfectly closed joint with no gaps. The result? No visible joints, no delamination, and no fiber swelling once the product has been painted. This is an expertise we have honed in the demanding door and window manufacturing industry, where precision and attention to detail are non-negotiables.
Profiling
Our state-of-the-art equipment enables us to achieve machining accuracies four times better than the rest of the industry. Each workstation is linked to our ERP system, which provides us with drawings, critical dimensions and tolerances on the profile being manufactured. Dimensional control is followed continuously throughout the manufacturing process, and template gauges are used to ensure dimensional consistency. These rigorous standards result in uniformly dimensioned wood parts, no matter how long ago they were manufactured.
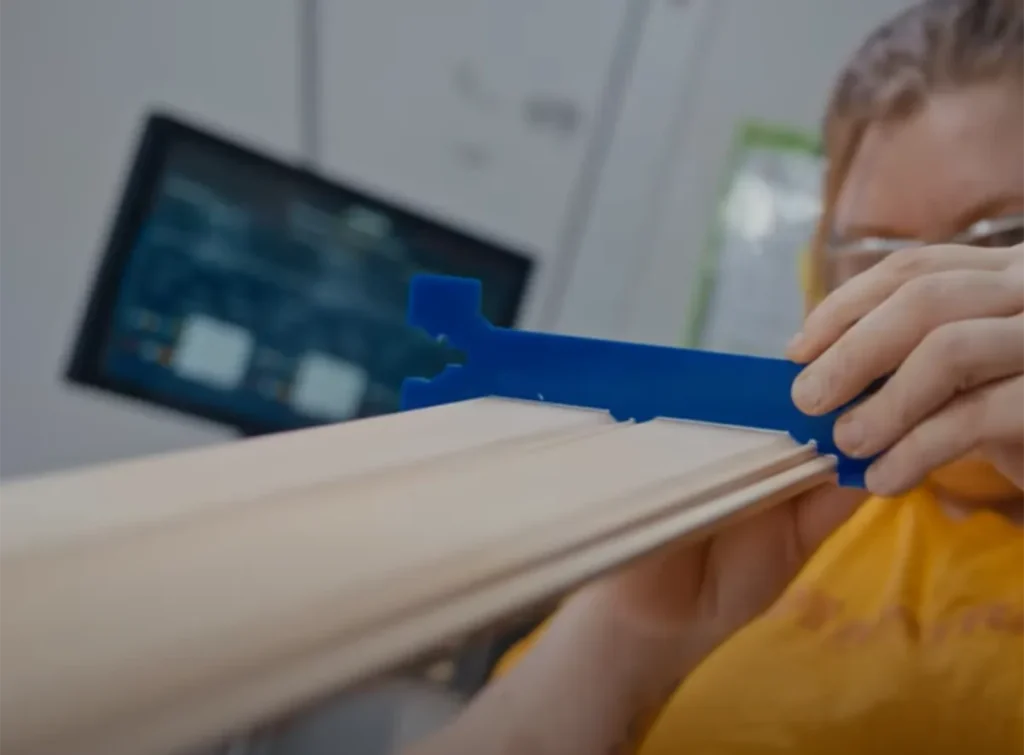
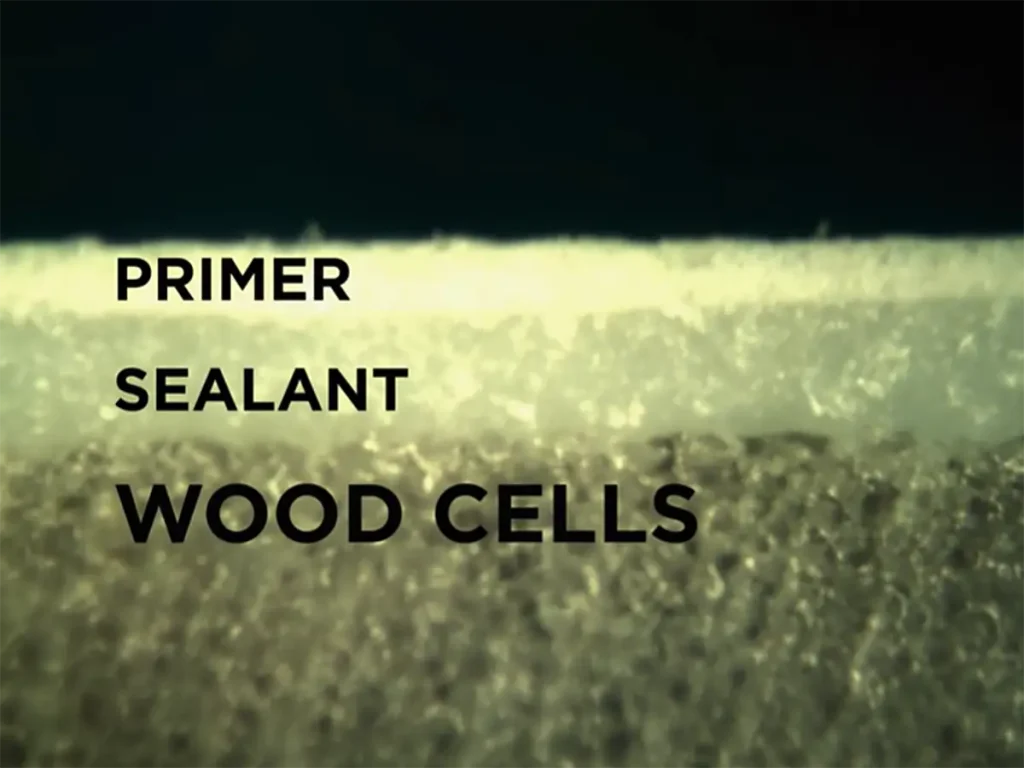
Finishing with Our Patented PrimeLock Technology
Our process ends with perfectly sealing all four sides with our proprietary PrimeLock Technology. Each individual layer of sealant is dried with UV lamps to lock in the strong joint and create an impermeable barrier from the elements. Once the sealing process is complete, a topcoat is applied to the back, sides and visible face. This additional coat of paint acts as a bonding agent between the UV sealer and the finishing coat applied on site. Boards are smooth and easy to install because of sandblasting between coats and precise jointing.
Quality Control
You can rest assured each one of our products is tested to the highest industry standards to provide you with high-performance wood trim you can install with confidence. Our joints, lamination and finishing are tested to ASTM D5572, ASTM D5751 and ASTM D3359, setting us apart from other manufacturers. Our lab is a center of expertise in which we can carry out research and development to improve the performance of our products and better understand the conditions that can affect them.
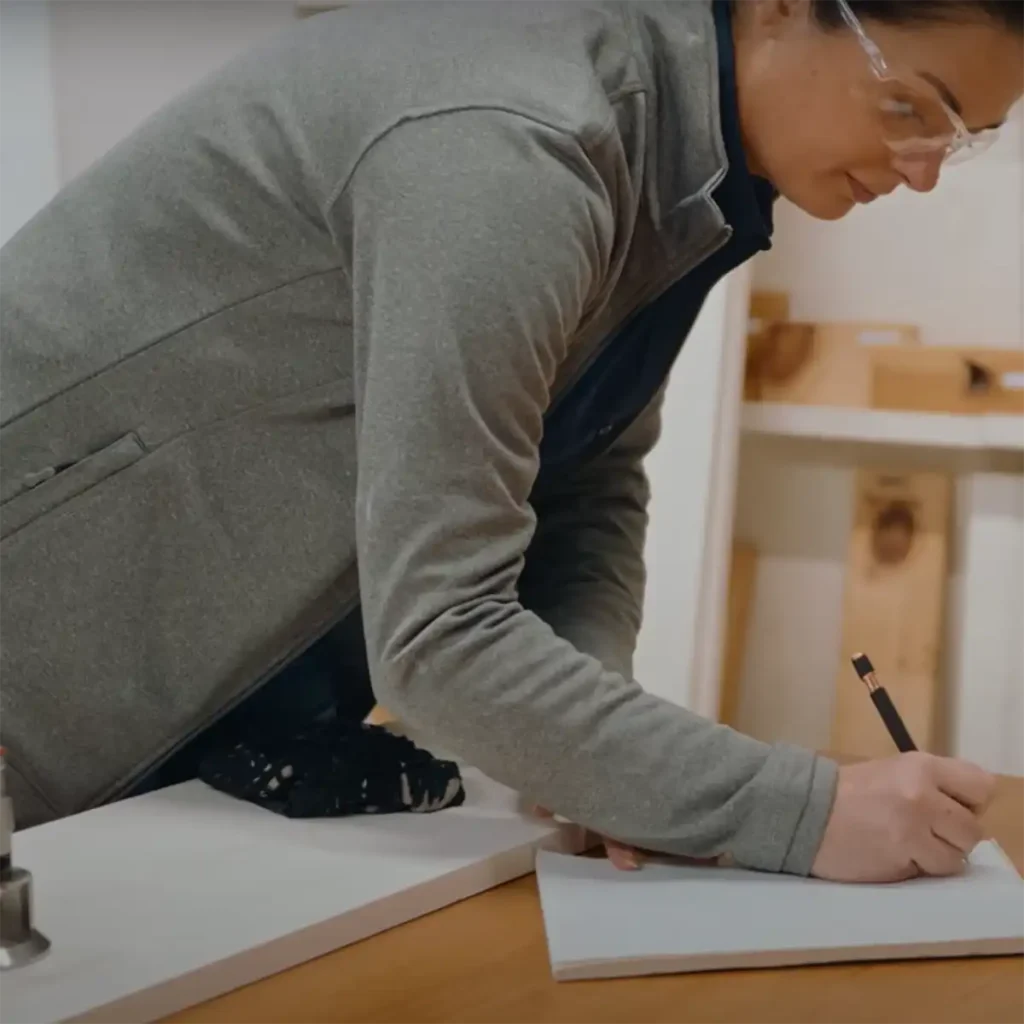